Brick, Stone, and Vertical Stamped Walls
Brick, stone, and manufactured stone are a perfect complement for ICFs. And while just about any exterior finish imaginable can be applied to ICF walls, brick, stone and siding are also extremely popular, especially in residential construction. They harmonize well with textured acrylic finish systems (TAFS), and as an added benefit, it’s usually easier and cheaper to apply these finishes over a foam substrate than a conventional wood-framed wall.
This two-part article shows how these finishes are applied, as well as tips and tricks to help the job go more smoothly. This installment focuses on brick, stone, manufactured stone, and vertical stamped walls. Siding will be discussed in the February issue.
Brick or Stone
The key to a brick or quarried stone façade is installing a steel-reinforced concrete brickledge. This ledge should be at least 4 inches wide and poured monolithically with the rest of the wall.
Nearly all major form manufacturers make a brickledge block specifically for this purpose. Some use a “taper-top form,” in conjunction with a smaller core size above it to create the ledge. As a last resort, builders can use a combination of hot knives, plywood, or removable steel forms.
Reward Walls is unique in offering a specialized steel reinforcer for it’s line of brickledge and taper-top forms. Called the xLerator, the one-piece wire reinforcement simply drops into the pre-formed slot in Reward’s ledge and taper top form. No tying or lapping is required.
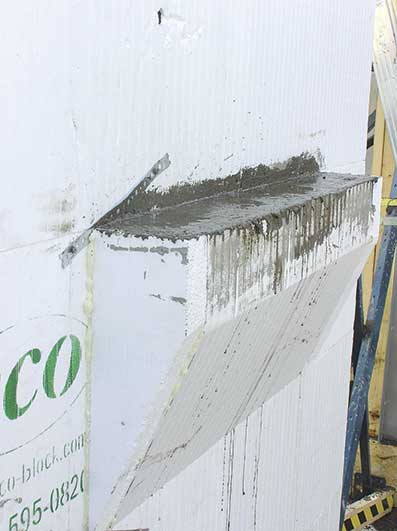
Brick and real stone require a brick ledge, which can be a specialty block (above) a taper-top (below) or made from scratch (bottom).
Rod Spellman, who has worked with ICFs since 1992, says he uses 9-inch-wide rolls of Blueskin for waterproofing both the brickledge and the window and door penetrations. “It’s wide enough to stretch from the nailing flange of the window 6 to 8 inches onto the foam,” he says. “I’ve never had any problems with it.”
Once the flashings are in place, stacking the wall is no different than any other method of construction. In most cases, there is no need to install a vapor barrier over the entire wall, as in frame construction, since foam and concrete do not rot or support mold growth.
Because of the weight of brick and stone (about 50 lbs. per sq. ft.) the mason will need to use brick ties to secure the façade to the wall. Spellman uses galvanized brick ties and treated 2-inch screws to attach the ties to the furring strips at the spacing specified by code.
Code also specifies a one-inch air gap, minimum, between the brick and foam. Real stone usually doesn’t require the air gap. Your form manufacturer can provide details and drawings as needed.
Spellman says he avoids a lot of problems by hiring experienced masons who know exactly how to build. “I use professional trades so I don’t have to babysit them,” he says.
Manufactured Stone
Manufactured stone, sometimes known by its trade name of cultured stone, is applied quite differently than real rock.
Because this material is quite lightweight—it weighs only one-fourth as much as quarried stone—it doesn’t need a brickledge to rest on. Brick ties are also eliminated. Instead, the stones are cemented to the wall using mortar.
Jim Eggert, a Connecticut-based contractor, applied 4,300 sq. ft of manufactured stone to a client’s castle-themed home this summer. (See ICF Castle in Connecticut in the June 2006 issue). Eggert writes, “We wanted to roughen the wall surface with a foam rasp and skip the metal lath, but the manufacturer… indicated that this method was only acceptable for interior work.” Because the manufacturer required the mesh to validate the warranty, Eggert installed it, using around 40,000 screws before the project was completed.
Some contractors, however, do adhere the faux rock directly to the foam on exterior applications. Journal of Light Construction published a story outlining the process in the June ’05 issue of their magazine.
“The recommended approach calls for a weather-resistant membrane such as 15-pound felt to be applied first over the foam board,” the writer states, “followed by a layer of expanded metal lath and a Portland cement scratch coat. The manufactured stone is then bonded to the scratch coat in a 1⁄2- to 3⁄4-inch-thick mortar bed and pressed firmly in place to squeeze out excess mortar and any air pockets.”
“[Project builder Todd LaBarge] reasoned that while eliminating air pockets is important, there’s no practical reason to install a moisture barrier over an ICF wall, because it isn’t susceptible to fungal decay. And metal lath, while entirely appropriate over an applied foam sheathing, is unnecessary as a structural base over ICFs, since the rough-textured EPS foam provides plenty of ‘tooth’ for the mortar to key into.”
LaBarge used the conventional “bottom up” method so that each course would be supported by those below. “We jointed the stones as we went along using a tuck pointer, then brushed the face clean of excess mortar,” he writes.
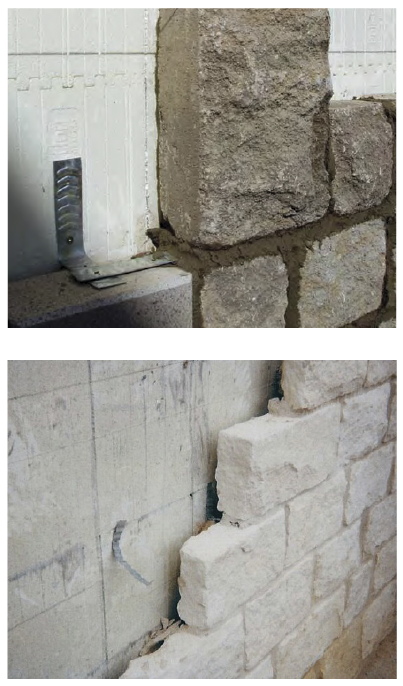
Brick requires a minimum 1-inch air gap (below left). Stone can be applied with an air gap (above) or in direct contact with the foam (top). Both products must be structurally connected to the walls with brick ties.
Eggert applied his finish from the top down. “The main reason is so you keep the stones as clean as possible because they won’t take much abrasion from cleaning brushes,” he says.
Eggert used a type S mix. LaBarge used type N, which has more lime. Both recommend using an acrylic admixture that enhances the mortar’s initial stickiness and ability to bond to both concrete and polystyrene.
Vertical Stamping
Perhaps the most versatile exterior finish is stamped, stained concrete. “There are no limits,” says Stanton Pace. “Any look that you want to achieve, you can.” Pace developed a product called Fossilcrete specifically for vertical applications. “It can create anything from a conventional stucco look to quarried stone, river rock, or even weathered wood,” he says.
Flex-C-Ment, by Yoder and Sons, is another option for vertical overlays. “It’s simply troweled up onto the interior or exterior walls, where it can be stamped and hand carved,” says Gregg Hensley, a sales representative for the company. “It can be applied from a half inch up to three inches thick.”
ArcusStone Products, LLC makes a troweled-on finish that exactly replicates the look of cut limestone. “It’s made with real limestone, so it looks better with age, not just older,” says Bill Tott, technical director for the company. “It can go from really smooth to travertine or rough cut.”
Pace is currently finishing a 20,000 sq. ft. house with Fossilcrete using his Great Wall of China stamp. (The stamp is an actual imprint of the oriental landmark, made during a “covert operation” to the communist country.) The four-story home, which will be featured in a future issue of our magazine, features an 8-12 pitched concrete roof, which is also stamped with Fossilcrete to replicate clay tile.
“The advantage of our system is getting a very authentic look, at a very high rate of production, at a lower cost to the builder,” he says. “It creates a monolithic finish that is completely waterproof and fireproof. It eliminate ties and mesh, but is incredibly strong and will not fail.”
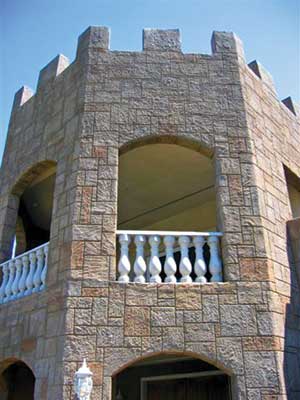
Vertical stamped and stained concrete can be virtually indistinguishable from real stone, even from a few feet away.
Pace says his product can be priced the same or slightly lower than manufactured stone, but jobs can be completed in half the time. At the World of Concrete Mega-demo in 2005, he and two assistants applied 160 sq. ft of vertical mix to a depth of ¾ inches and then stamped it in under an hour.
Yet Pace claims that the product’s greatest advantage is “the ease and freedom where you can apply the product.” Tricky areas, like where the fascia, soffit, and column come together are easily finished with his product. “Fossilcrete lets you build around the problem,” he says.
His product is also being used on a 13,000 sq. ft. house with a finish that replicates large blocks of chiseled stone. With individual blocks measuring two feet by three feet, he points out that the look would be extremely difficult to create any other way, even with manufactured stone.
Vertical stamped concrete blends well with other finishes, too. “Even if you use a regular Dryvit or something for the walls, this product can create fantastic window treatments,” says Pace.
Application is easy. “If the block is in good shape, no preparation is necessary,” he says. “If it’s yellowed, rasp it down to good, clean, white foam.”
The bond coat is rolled, sprayed, or brushed on, and then a scratch coat is applied, either with a trowel or with a hopper gun. Once the scratch coat is dry—20 minutes or so, the stamp coat gets troweled on. The entire process takes less than an hour.
The mix is stamped and detailed before it dries; applicators have up to 30 minutes of working time. A water-based concrete paint can be used to accent individual stones.
The Flex-C-Ment process is similar. Hensley says that the reason the scratch coat must harden before the color coat is applied is to ensure you don’t carve all the way to the foam. Flex-C-Ment offers mixes with integral color and a full array of stamps and skins.
Unlike Fossilcrete or Flex-C-Ment, ArcusStone materials are not direct applied. Standard EIFS mesh, embedded in a cementious base coat, is first applied. A bonding agent is then rolled on before finishing with the top coat. The company offers two different finish products. Arcus Plaster is easiest to apply. It can be troweled on, or spray-applied and troweled later. Arcus Stonecoat has larger aggregates—up to ¼ inch—so it needs to be applied thicker. The company also offers admixtures for using the product below grade.
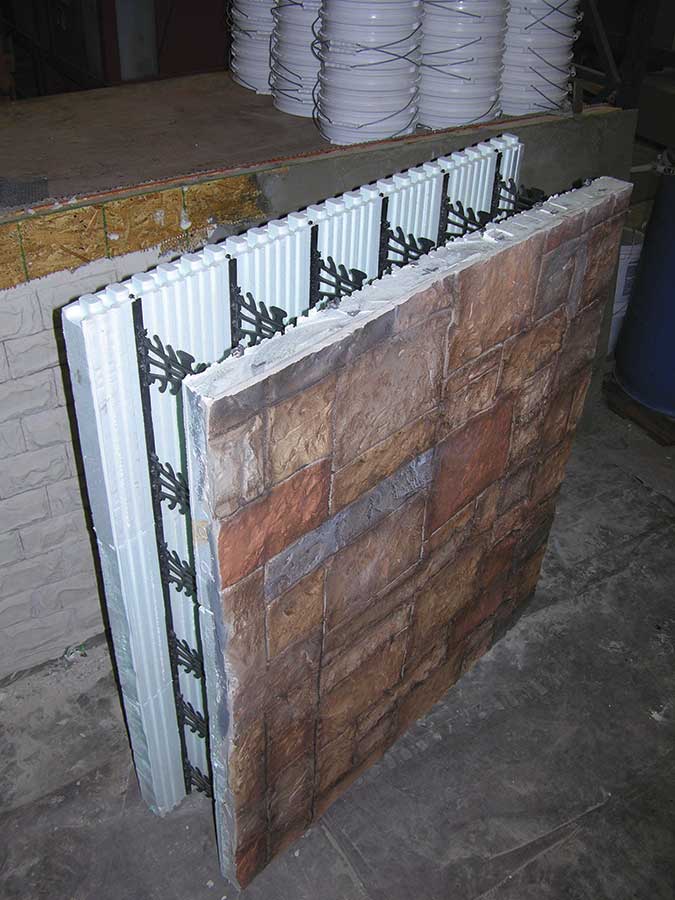
Fossilcrete is so lightweight that it eliminates ties and mesh, but is incredibly strong and extremely realistic.
“We’re considerably less expensive than real stone,” says Tott. “[With quarried stone], you have to bump out foundation, install tiebacks, and make sure the wall reinforcing meets code. Our product weights only 3 lbs per sq. ft. (applied at 3/8”) and costs typically range from $12 to $15 sq. ft. installed.”
Pace, at Fossilcrete, says ICF walls are a perfect substrate for vertical stamping. Applied properly, the technique is durable, easy to apply, can create unlimited styles, and offers significant cost and labor savings.
“Every time an architect, designer, or homebuilder looks at what to do on walls, this is a viable option,” says Pace.
Regardless of whether you choose brick, stone, or vertical stamped overlays for your next project, remember that all of them involve cementious materials. They need to be kept at a minimum of 40° F (4° C) during the work and for 48 hours afterwards, protected from rain, and not allowing work on the other side of the wall until the mortar or overlay has cured sufficiently.
Part II of this story, to be published in the Feb. 2007 issue, addresses how to apply siding.
I’m looking for the best pool finish on icf
I have a ICF house and sick and tired of having the stucco pooch out and crack and have to be repaired. Lately most of the damage is below the windows in a 3′ area above the ground. What can be put on on the sides of the house at the bottom which is thicker like concrete that will stop this. I want it to look good too. I’m a healthy 84 year old woman with a husband in a nursing home. I’m tired of worrying about this. Is there a frame thick enough that cement like material be put in that can be held to the ICF and never crack again. I don’t care if its smooth or whatever. Water is sweating behind the stucco that must be stopped this damage.
Thanks for your help.